Product Name:
Oil HeaterBrand Name:
Hot Oil Boiler, Thermal Oil Boiler, Hot Oil HeatersApplications:
Asphalt Industries: For asphalt production, waterproofing membranes (such as bituminous membrane), heating swimming pools, emulsifying and heating heavy oil materials in large tanks.Wood Industries: For manufacturing and drying wood veneers, particleboards, and MDF.
Textile Industries: For heating dyeing machines.
Chemical Industries: For heating autoclaves and chemical reactors.
Food Industries: For the production line of chips, soda and candy production, frying items, and vegetable oil factories.
Leather Industries.
Cement Industries.
Motor Oil Industries.
Structure and Operation:
To provide heating and heat transfer for heating bitumen, an oil heater is used. In this device, thermal oil is heated to approximately 150 to 200 degrees Celsius and transferred to the bitumen flask for heating. The hot oil circulates through a coil installed inside the bitumen flask, and by circulating the hot oil, the bitumen in the flask is heated to the required temperature. For heat supply to the oil inside the coil, the oil heater is equipped with the necessary burner and control equipment to ensure safe operation and automatic heating and oil transfer. This device transfers heat to the bitumen flask, double-walled pipes, and mazut flask in the asphalt factory through the circulation of hot oil. Oil heaters are usually manufactured in heat capacities ranging from 250,000 to 1,200,000 kilocalories and with an expansion vessel capacity of 250 to 300 liters. The oil heater is fully controlled by thermal PT100 sensors, oil pressure control, and pressure drop leaks, providing a very high level of safety.Components of the Oil Heater:
A complete system or package of hot oil for proper, correct, and safe operation includes the following components:1-Hot Oil Boiler
2-Burner
3-Circulating Pump
4-Power Supply
5-Feeding Pump
6-Expansion Vessel
7-Control Equipment
8-Control Panel
9-Gas Separator from Oil
10-Valves


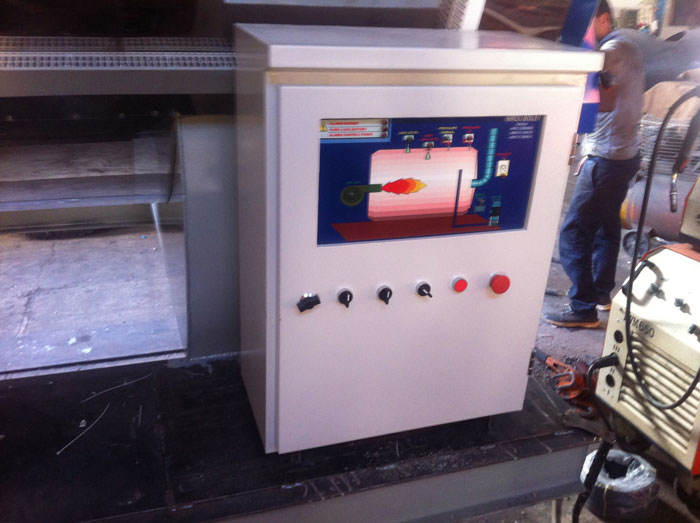
